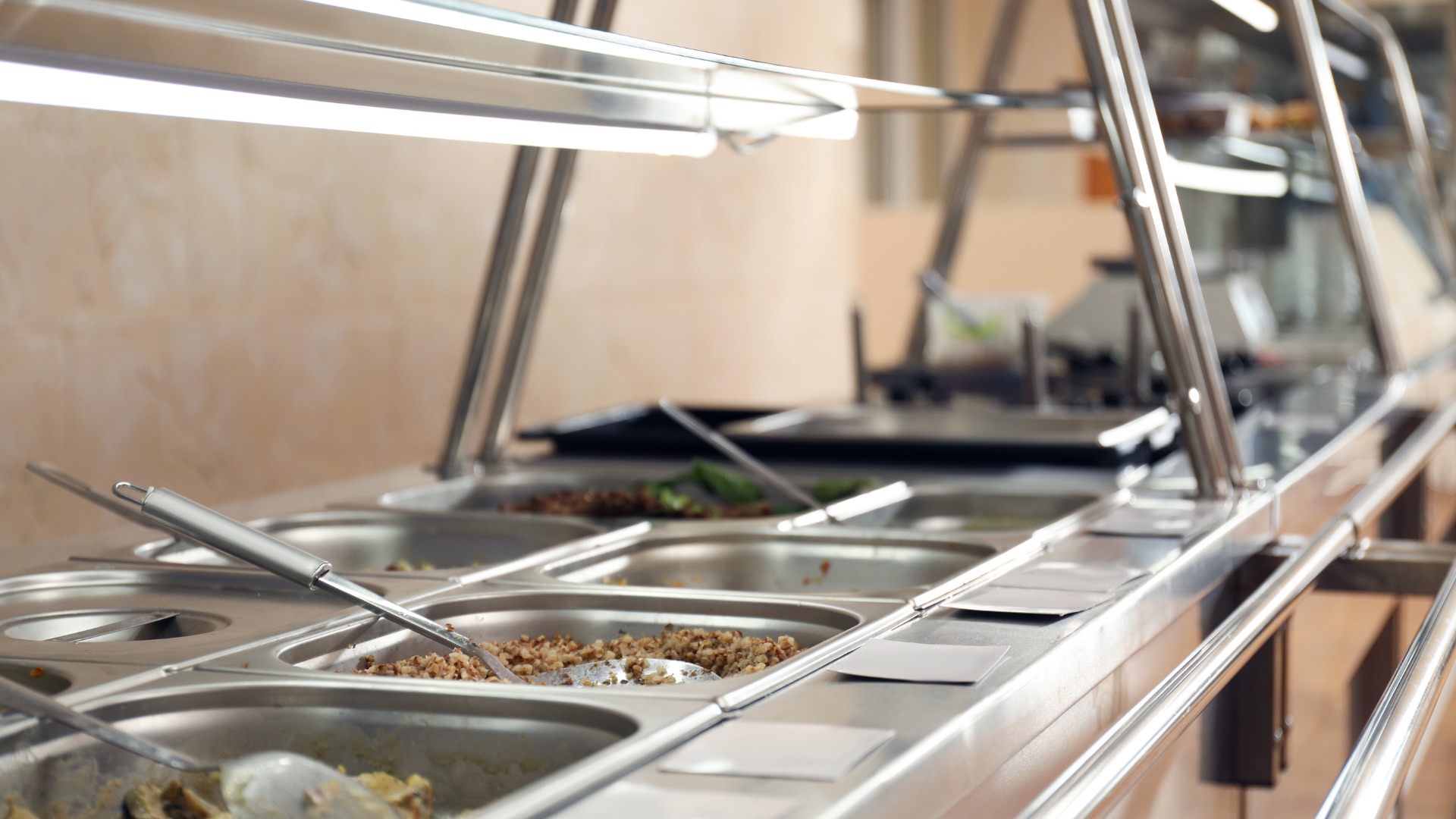
CKC Good Food is a collaborative food service provider based in Minneapolis and Saint Paul, Minnesota, USA. They supply and deliver nutritious meals to schools, summer camps, residential homes and more, in addition to partnering with clients for catering and event services. With the help of our barcode inventory system, the team has been able to cut inventory management time by 60%… 😲 Find out how Orca Scan transformed their daily operations👇
The challenges: struggling to find the right solution!
Since starting his role at CKC Good Food, Steve tried several inventory management systems but couldn’t find any that suited his needs. One system would require too many procedural steps to do simple tasks; others didn’t have enough features or would require additional, specific barcodes to be attached to products for tracking.
Steve even attempted to digitalise his inventory process by using Google spreadsheets. He would ask staff to count stock and then manually enter it into a shared spreadsheet to monitor and track all deliveries and products in the warehouse. This process was met by a tonne of human errors, and sometimes, they’d even enter data into an old spreadsheet by mistake!
Unfortunately, due to the nature of the food service industry, deliveries and shipments move so quickly in and out of the warehouse that searching for an inventory system was not only wasting his time but it made it harder for the team to envision using a digital inventory system at all.
A good thing about Orca is that it’s always moving in the right direction. The last system I used, nothing was going to change and nothing was going to get any better. It was just a waste of time staying with themSteve FlemingInventory AnalystCKC Good Food
A little bit of context: Meet Steve, Head of Inventory Management
We met with Steve Fleming, Inventory Analyst at CKC Good Food, to discuss how he uses our Inventory Tracking solution and how Orca Scan is providing value and supporting his teams daily.
Each day, the team prepares over 25,000 meals to over 200 client locations, meaning they provide over 125,000 meals a week…😲👏 These meals are created to be healthy, nutritious and are designed to ‘inspire joyful eaters’.
Steve is responsible for putting efficient systems in place to monitor and track deliveries, stock in the warehouse and shipments so that the team can prepare and ship final products off to client sites. However, he was unable to find a long-term, efficient solution that was easy to implement, understand and use daily… until now 👀
The beauty of this system is that we can use the labels already on the boxSteve FlemingInventory AnalystCKC Good Food
How Orca Scan provides a solution: reduce time spent manually counting stock
Steve implemented Orca Scan’s Inventory Tracking Solution to take control of stock counts and digitalise the process to save time and increase efficiencies within the team. He uses Orca Scan to track all the food that gets delivered into the warehouse from fresh fruits and vegetables, to meats, and dairy, and non-perishables. They also track the manufacturer, brand name, food type - i.e. breakfast food or lunch item - and case size, quantity, and cost.
Some items come prepackaged, whilst other ingredients come in larger quantities that the team decants and measures out into the correct weights needed by their chefs to prepare food before sending it out to client sites to be cooked.
Stock counts occur daily, as the turnover of food is so high, meaning their data is only valid for a few hours…🤯 Steve typically does a count at the end of each day to determine what stock they have ready to be prepared and used the next morning. Another reason why a digital database was so essential for Steve and his team!
With these counts, Orca has provided the team with a more accurate, real-time count of all stock on hand in the warehouse, allowing them to determine what needs to be ordered…which also means much less food waste👌
Formulas
Steve was a big fan of our new formulas feature, using it to quickly and easily work out the cost of each case by selecting the weight column, desired calculation (✖️➕➖➗), and quantity column to complete the calculation and get the final cost of each case. Once he had it set up, that column will auto-populate when the information is in the sheet. One less thing for Steve to worry about.
It sounds simple, but it’s so important. In the past, we would have had to build the formula into the spreadsheet every single time it was exportedSteve FlemingInventory AnalystCKC Good Food
Has the solution been successful?
Since implementing Orca Scan, Steve has seen time savings of over 60% 👏 🤯
The team can now manage deliveries and stock through our handy mobile app by scanning product barcodes and watching as this data is extracted into set columns in their Orca sheet. The solution is much faster, allowing the team to complete delivery and stock counts much more efficiently, rather than spending hours of time using pen-and-paper checklists and manually entering data into spreadsheets.
Orca Scan has made a huge difference to Steve and his team at CKC Good Food, benefitting stock counters and positively impacting other members of the business, like warehouse staff, who can now easily access the correct data when they need it.
The beauty of Orca is its flexibilitySteve FlemingInventory AnalystCKC Good Food
Thank you 💛
Thank you to Steve and his team at CKC Good Food for chatting with us about how Orca Scan has helped save masses of time and increase overall team efficiency 🙌 That’s what we love to see.