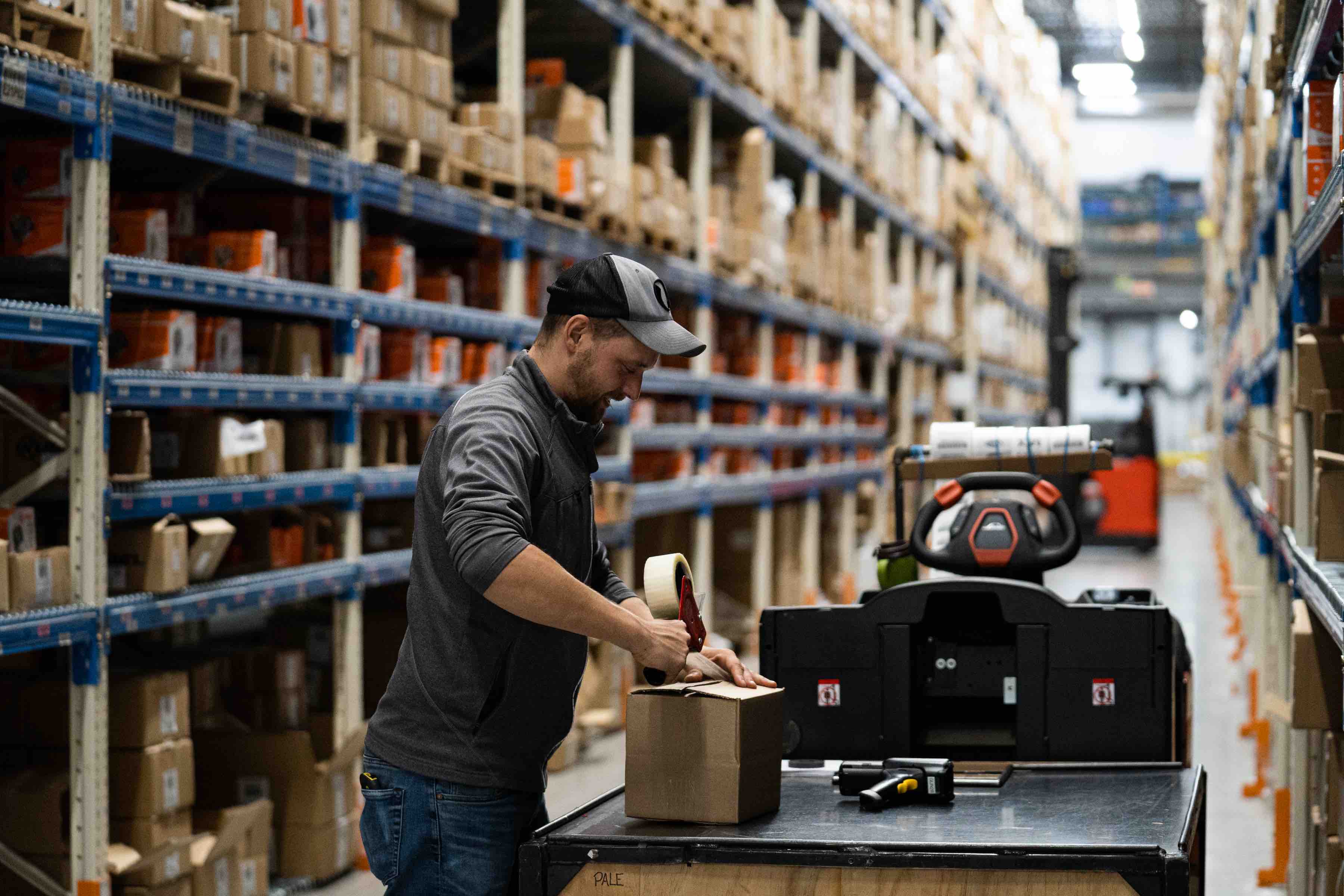
Transit inc. is the largest auto parts warehouse in eastern Canada. Operating since 1971, they have a catalogue of over 20,000 car parts and accessories. By implementing Orca Scan, they have transformed the efficiency of their returns department, reducing the amount of time spent on returns by 169%, and freeing up their team to do their best work and reach their true potential. Here’s how they did it…👇
The problem…
Transit was using a pen-and-paper method to track and process their returns for many years. However, it was producing a lot of mistakes from lost products, miswritten forms and bad handwriting…❌✏️
The whole process was becoming increasingly time intensive, inefficient and started to impact staff morale - completely at odds with Transits values. So Pascal took the initiative to implement a barcode system to simplify the process, improve efficiency and save time.
I’d never go back to our old systemPascal OuelletPrincipal Account Manager & Technical ExpertTransit inc
A little bit of context…
Transit specialises in importing and distributing car parts across Canada through a B2B model. They have recently started experimenting with selling directly to consumers through channels like Amazon and eBay.
Like many industries, they noticed that they were suffering from employee shortages following the COVID-19 pandemic, and paired with the high staff turnover, the issues surrounding the returns process was impacting all departments👎
How has Orca Scan provided a solution?
Pascal started implementing Orca Scan using smartphones and Bluetooth scanners, introducing a new way to process returns.
It’s a game changerPascal OuelletPrincipal Account Manager & Technical ExpertTransit inc
When a package is received, employees simply scan the package into Orca Scan using the UPC barcode on the product.
Using triggers, when the scanning is complete, an email is automatically sent to the sales department. Sales can then access all the information required for them to generate a return and place the product back in inventory 📦. At the same time, an acknowledgement of receipt is sent to the customer to confirm that what has been processed is the same as their returns report.
Orca Scan not only helped streamline the returns process but also helped the team manage their inventory.
Was the solution successful?
It previously took a couple of hours to process each pallet of returns; since the implementation of Orca Scan, that’s down to 10 minutes⏱️✅
The process is now so fast and easy that the returns department now only needs part-time employees, freeing up workers to do more enjoyable tasks.
This not only improves the quality of work and increases job satisfaction, but it’s made Transit more efficient, too - since Orca Scan, they’ve not had a single resignation from the returns department, saving time and money on salaries and new hire training.
There have been other benefits too. Introducing Orca Scan has not only helped the company turn paperless but has also added a layer of accountability. They can now clearly see exactly what’s been returned and at what time and are able to deal with any missing products or mistakes in real time. This has reduced the number of complaints and disputes between the client and the returns department - especially important when dealing with bigger clients where there is a lot of back and forth with products.
It’s not very often we come across a system that we use daily in multiple warehouses, and it’s totally reliablePascal OuelletPrincipal Account Manager & Technical ExpertTransit inc
Transit is now using Orca Scan at the main warehouse and for customer pick-up locally… in fact, it’s been so successful it’s been expanded to two other depots 🏢🏢 🎉
Thank you to Pascal and the team at Transit for sharing their story. We are very grateful 🙏
Looking for a similar solution? Book a demo now!