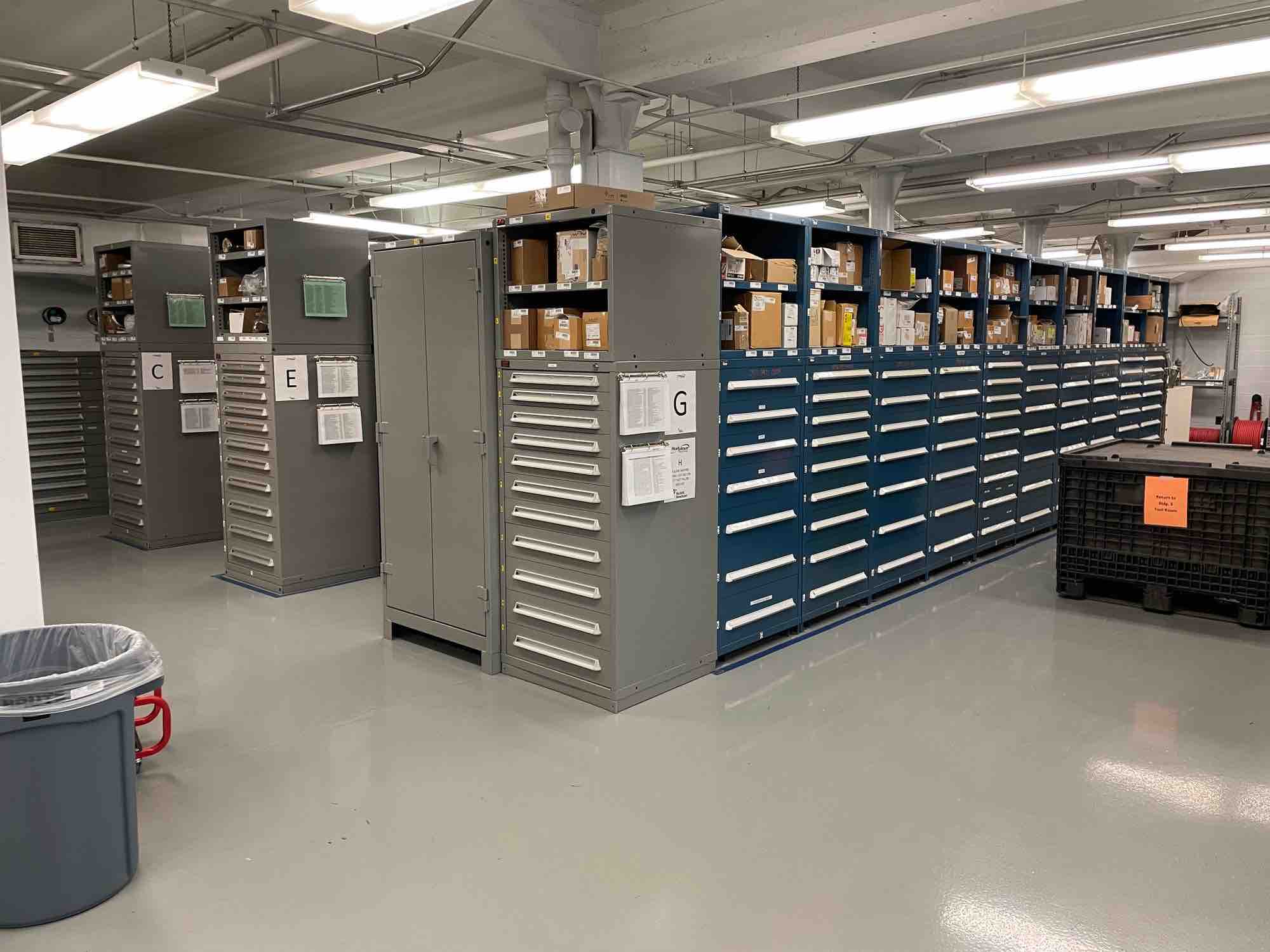
For more than a century, Mead Johnson Nutrition (part of the Reckitt Benckiser) has led the way in developing products designed to help meet the nutritional needs of infants and children. Producing a broad portfolio of leading formula brands, including Enfamil, and more than 70 products, they are the only global company focused primarily on pediatric nutrition.
The problem…
In 2018, Alex Albright, Associate manager of Non-production Spend, took on responsibility for the production storeroom at the Enfamil factory.
He noticed the team were using a pen and paper method for daily inventory, which had to be repeated each time an item changed location 📝.
This was becoming time-consuming and ultimately costing the business ⏱
Alex’s goal was to improve the efficiency and accuracy of this process. He knew he needed a digital solution, and that’s when he found Orca Scan.
I chose Orca Scan because of its ease of use and instant implementationAlex AlbrightAssociate Manager of Non Production SpendEnfamil
A little bit of context…
Since 1915, Enfamil infant formula drink has been produced in Evansville, Indiana. The site has 5 production areas with each needing 20,000 unique spare parts. It has over 300,000 parts in storage, 19,000 storage locations and over 800 people on campus each day, pre-COVID.
With so many moving parts, Alex needs to know exactly where parts are stored, when they were received, how many are in stock and who was the last person to see them.
This was a challenge using the current model.
How has Orca Scan provided a solution?
Kiran Chandrapaul of MSN Air Service, claimed once he started using Orca Scan, he could “see new implementations for it everywhere”… This couldn’t be truer for Alex, who has simplified several processes to increase visibility and efficiency throughout the facility using Orca Scan 👇
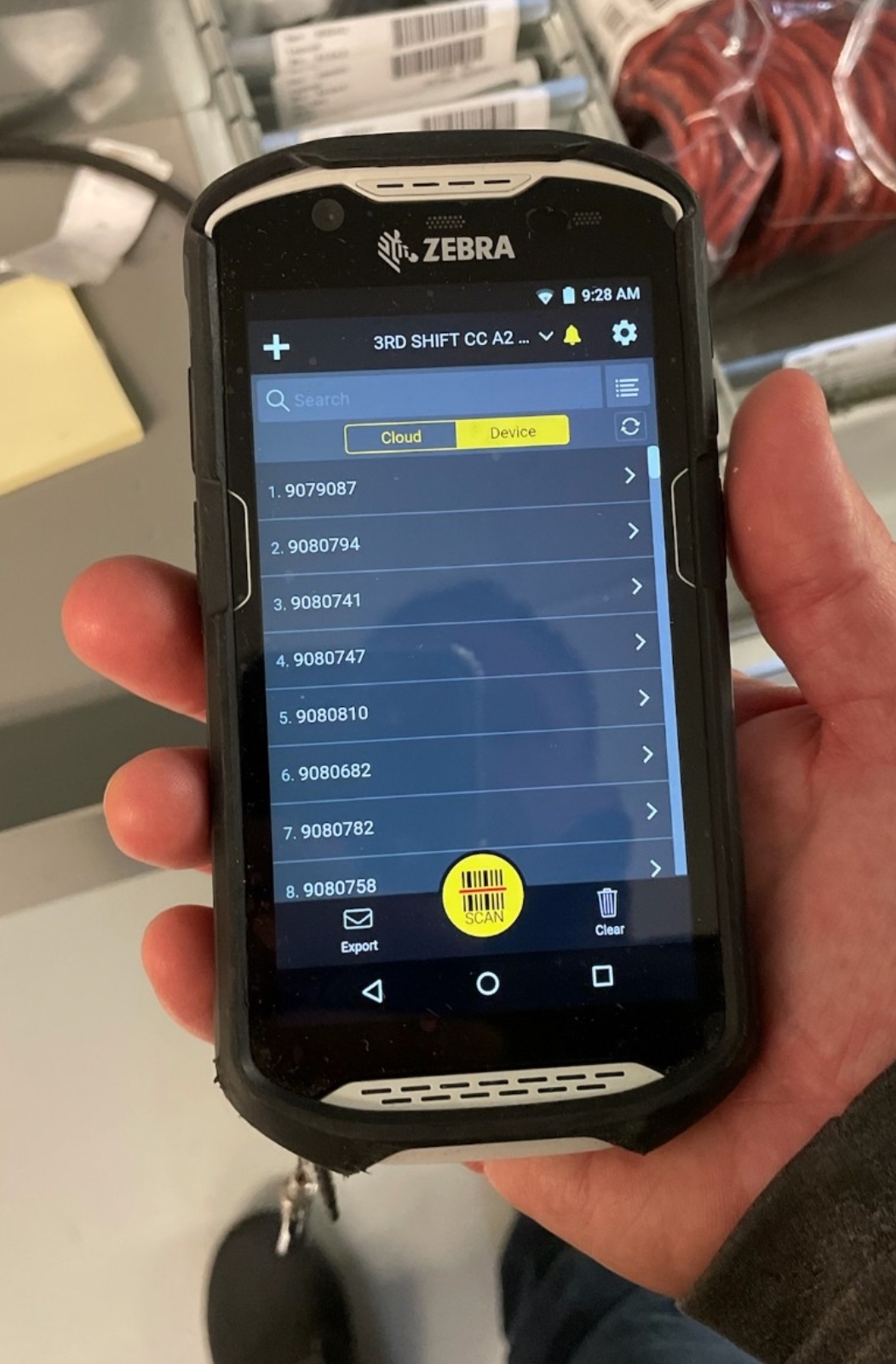
Checking things into the storeroom ✅
Orca Scan is used to scan the 60+ packages that arrive on location each day. The tracking number and location of the parcel is recorded and automatically sent to Alex via email and exported to an Excel sheet in real-time. With 52 possible delivery destinations on-site, this significantly reduces the amount of time needed to find parcels.
We didn’t have any way of tracking anything that was received in-house prior to using Orca ScanAlex AlbrightAssociate Manager of Non Production SpendEnfamil
Storeroom inventory sheet 📝
Once the parts have been delivered and transferred to the storeroom, they are scanned again to keep track of inventory levels. The storeroom attendant maintains an up-to-date inventory cloud sheet with the location and image of each item so it can be easily identified and located.
Cycle counting 🔄
Each morning, a cycle count is undertaken on at least 1 storage area (approx, 200-300 parts) and is exported into an Orca Sheet. The store attendant also scans all items in the storeroom, in that location, and cross-references. Using Orca Scan, the team can undertake this task 50% faster than before.
Orca Scan has drastically improved the efficiency of our cycle counting and can report back with details on all item numbersAlex AlbrightAssociate Manager of Non Production SpendEnfamil
Ease and speed of locating parts in the storeroom 📍
The Evansville facility has up to 19,000 different storage locations, so the ability for the team to find a part is vital when production is down. Parts are needed quickly, and time wasted searching for parts is frustrating and costs the business. The team are using Orca Scan to generate barcodes for each of the rows in the storeroom, when scanned it lists what is stored there, the item number, description, and manufacturer’s part number.
Tool location 🛠
In response to workers feedback, things are often moved around to be in the most efficient location.
Each item on site has a dedicated barcode, and when an item is moved, the barcode is scanned and a ‘location updates’ sheet is updated with the items previous location, new location and quantity.
This process helps to ensure that items, parts, and packages are able to be found at all times.
Charging out items ❌
Once items have been located, team members are required to use a dedicated Orca Scan sheet to charge out the item they need. They simply put in the item number and follow the instructions to include a description of why they need the part, what department they need it for and finally the name of the person charging it out.
This keeps Alex aware of who made changes to the inventory and why.
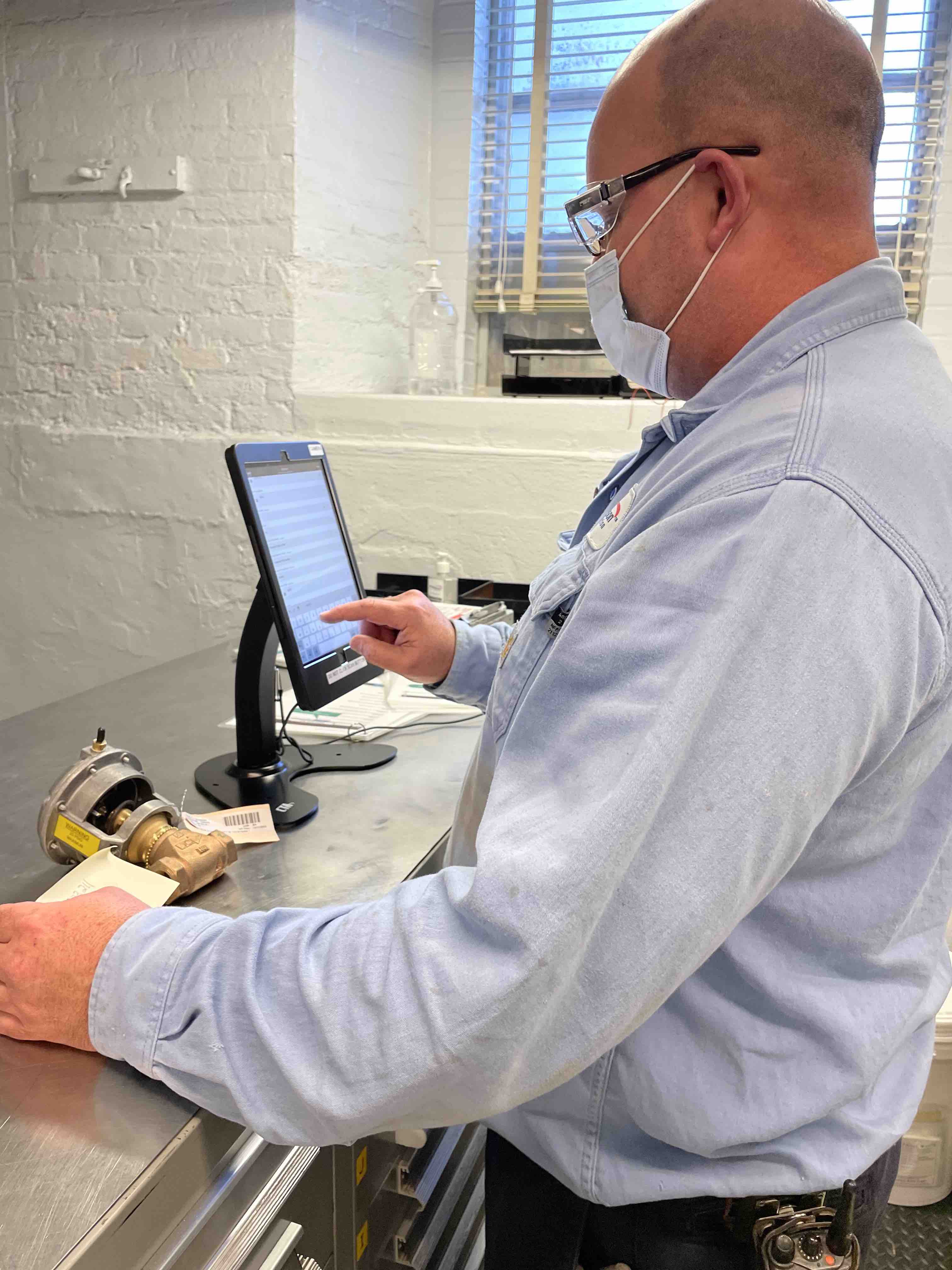
Was the solution successful?
Alex has been working with the Orca Team for over a year to digitalise the Enfamil systems which resulted in a huge reduction in paperwork and also helped the accuracy and efficiency of their inventory.
The implementation has been so successful that Alex is being tasked with rolling out his Orca system in other Enfamil sites…even better, there are still lots of new implementations to come in both the Evansville factory and beyond! 🚀
Even if the functionality doesn’t exist, I know that I can work with the Orca team to create something that will workAlex AlbrightAssociate Manager of Non Production SpendEnfamil
Thank You
Thank you to Enfamil for sharing their story and a BIG thank you to Alex for his feedback and work with us as we continue to improve Orca Scan 🙏
Looking for a similar solution? Book a demo now!