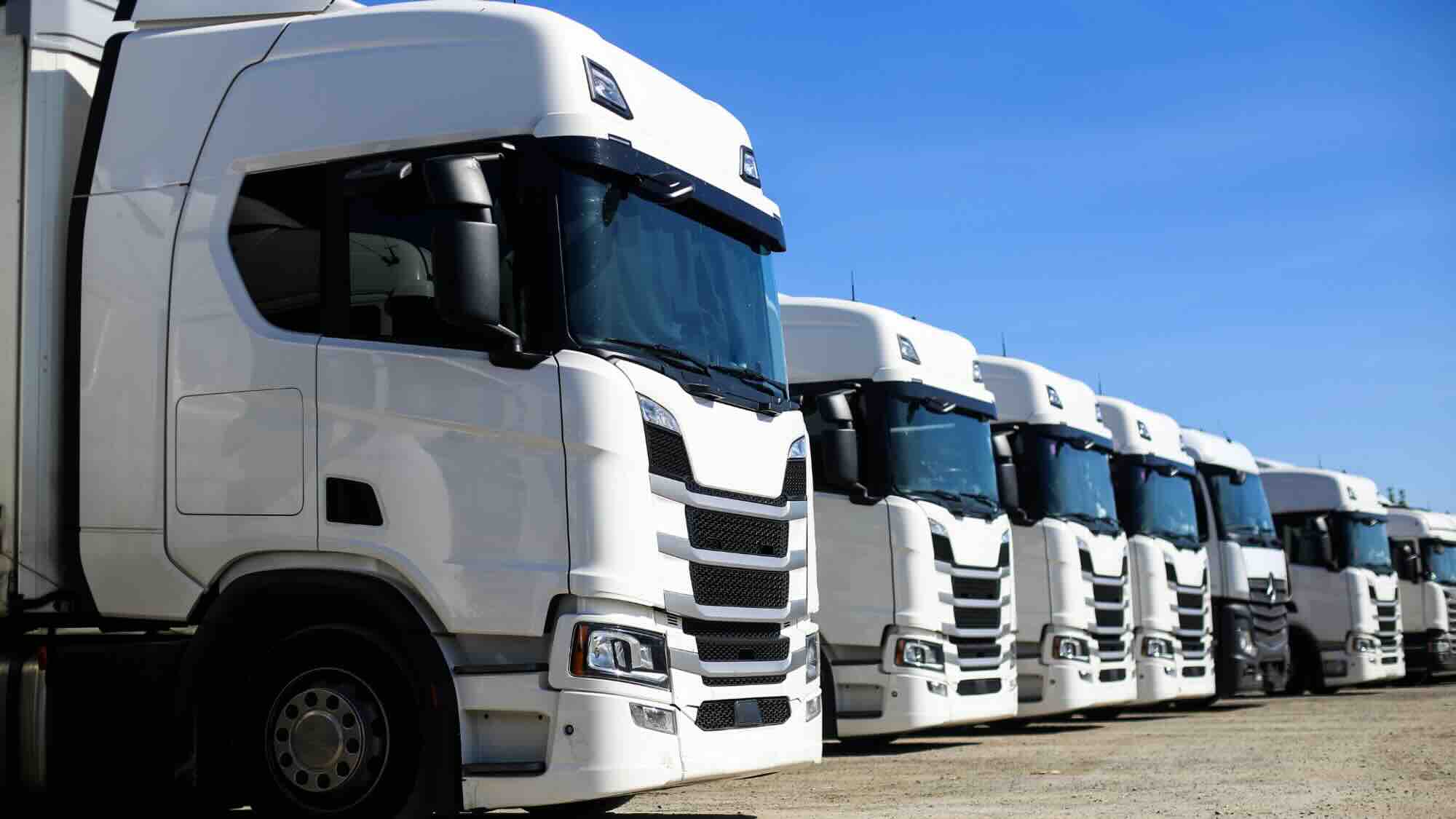
Lawrence David Ltd, a leading trailer manufacturer in Peterborough, England, saw huge financial benefits after implementing Orca Scan in 2020. They recovered finances, improved team efficiency, and decreased their carbon footprint.
Here’s how they did it 👇
The Challenge: Reduce loss and improve efficiency with weekly stocktakes
The Lawrence David team completes a weekly stocktake of vehicles on site. This stocktake involved around 800 vehicles, and it was clear that their pen-and-paper method 📝 was costing them time and prone to human error.
Additionally, they had no clear way of tracking the progress or status of customer orders without lengthy investigations across multiple storage sites—something needed to change.
If you visit the foreman’s offices, you would see stacks and stacks of paper, but all you’ll see now is a tabletDarren ChallenderGroup IT and Digital Transformation DirectorLawrence David Ltd
Darren was assigned the task of solving these problems. Although technology wasn’t the desired approach, Darren needed to find a solution that would not only reduce the financial losses but would improve the productivity, accuracy and efficiency of the whole process💡
Technology was a swear word before I joined. It was always a hindrance; it just didn’t work…but now it’s changing their business mindsetDarren ChallenderGroup IT and Digital Transformation DirectorLawrence David Ltd
A little bit of context: Meet Darren, the Group IT and Digital Transformation Director at Lawrence David LTD
For over 45 years, Lawrence David has been at the forefront of commercial trailer manufacturing. Their extensive experience within the industry, as well as their design and engineering expertise, has made them pillars of the haulage industry.
Orca Scan has changed the way we view technologyDarren ChallenderGroup IT and Digital Transformation DirectorLawrence David Ltd
Darren joined the company in 2020 during the COVID-19 pandemic. Sadly, the company was experiencing a significant loss because of errors in their stocktake. The team tirelessly ticked off products on pieces of paper for three weeks, inputting numbers into spreadsheets and exporting this information into their ERP system. Darren knew he had to make a change ⏩
How Orca Scan Provided a Solution: Improving Visibility, Quality and Accuracy for Stocktakes
Darren and the team generate a QR code for each of the vehicles on site, which includes a wide range of information like:
- VIN
- Job Number
- Works number
- Customer name
- Order number
They placed these QR codes on each vehicle’s chassis and scanned them with Orca Scan to ensure end-to-end tracking of assets.
Manufacturing process 🛠️
As parts arrive at the warehouse and are ‘de-stacked’, they are scanned into a dedicated Orca Sheet before moving into manufacturing. They are further scanned once the assembly is complete. This helps the team have greater visibility over the process of customer orders and has reduced the time needed to provide requested updates.
Quality checks ✅
Once manufacturing is complete, the vehicles are checked for quality control assurance. Using photo fields and triggers, any issues can be captured and shared with the relevant team to resolve.
When all quality controls are finalised, and the customer comes to collect their order, they use signature fields to sign orders out and mark them as ‘collected’. This solution has boosted their efficiency, saved time in the order process, and helped them tackle any issues before customer collections 🙌
The biggest thing is having the information in their hand at any time. They’ve all got phones and the Orca Scan app. They scan the QR code, giving them all the information they need without going to their office computer to look it upDarren ChallenderGroup IT and Digital Transformation DirectorLawrence David Ltd
Asset visibility 🔍
Using asset maps, Darren has significantly increased the visibility of all the vehicles across multiple site locations. As a vehicle moves through manufacturing, quality control and storage ahead of collection, the team must scan at each stage. The sheets have drop-down columns to ensure they capture all the essential information, including which driver signed it out of each step.
Weekly stocktake 📊
The team must attend every site each week and conduct a stocktake. All vehicles must undergo scanning and checking to ensure the information in the sheet is correct. Orca Scan’s Excel integration automatically exports this for analysis.
This solution allows the team to track workforce productivity, and the increased visibility has increased turnover in successful orders being completed 👏
Has the solution been successful?
Since introducing Orca Scan, the team have successfully reduced the time needed to undertake stocktakes from 3 weeks to just three days - a massive time-saving! ⏰ They have also seen an increase of over 50 vehicles a month being successfully collected by customers because of the increased visibility of stock and order status.
Saving time has also helped save money, and the team has been able to reduce any previous financial losses, resulting in a business surplus 🎉
One of the reasons I got my promotion was the digitalisation that comes with Orca ScanDarren ChallenderGroup IT and Digital Transformation DirectorLawrence David Ltd
Not to mention, the CEO and Owner of Wielton has hugely supported Darren, and as a result of his hard work, he was promoted to “Group IT and Digital Transformation Director” in 2022 👏
But he’s not finished yet; the project has been so successful that Darren is now expanding the use of Orca Scan across his international offices and sister companies.
A big thank you…
To Lawrence David Ltd, especially Darren, for sharing your story with us and explaining how Orca Scan has simplified the stocktake process and made the team’s life a little (or a lot) easier 🙏 We have loved working with you over the last few years to build a solution that will aid the company’s efficiency, and your feedback has been invaluable. We are very thankful 👏